Das Arbeitsprinzip des Spritzwerkzeuges
Das Arbeitsprinzip des Spritzwerkzeuges
Hoshen Präzision, die unserem Team die Zertifizierungen bietet, macht das komplexe Verfahren der Spritzgussform einfach, weil unser Team jahrlange Erfahrung haben. Hoshen Ingenieure werden Ihnen helfen, um die Zeichnung der Teile zu entwerfen, oder aktuelle Formen zu überprüfen. Es gibt fünf Kriterien, die währende des Spritzgießzyklus erfüllt werden müssen: Klemmung, Einspritzung, Abkühlung, Formeröffnung und Teileentnahme. Im Allgemein wenn die Abmessungen und die Qualität der Form gewährleistet werden, wird der Spritzgiesszyklus so schnell wie möglich durchgeführt.
Der Spritzgießzyklus beginnt mit dem Zeitpunkt des Formsschließens, kurz bevor die Führungssäule der Form zu dem sicheren Zustand gerichtet hat. Der Grenzwert der Geschwindigkeit und Druck wird zu niedrig eingestellt, um die versehentliche Beschädigung zu vermeiden. Wenn beide Hälften der Form hohen Druck erhalten, dann kann die Form schwere Dinge einklemmen.
Die Spritzgussform für Kunststoff verwendet die thermoplatischen Materialien(Kunststoff, der erweicht und verwirbelt wird, wenn er erhitzt wird) als den Rohstoff. Die Kunststoffe, die im Spritzgiessverfahren verwendet werden, werden bei der Temperatur zwischen 220° C und 270° C verflüssigt. Das thermoplastische Material, das in dem Spritzgiessverfahren eingesetzt wird, wird in der Form von kleinen Pellets angebot. Diese Pellets werden in den Behälter ausgefüllt, dann werden sie in den Lauf und der Spindelanordnung eingeleitet.
Der Schneckenkolben komprimiert und schmilzt den Kunststoff. Er verschiebt das Material in Richtung der Form. Er ist in drei Zonen eingeteilt, einschließlich die Zuführungszone, die Übergangszone und die Dosierzone.
· Zuführungszone-Wo der Kunststoff erst eingeleitet wird.
· Übergangszone – Nach der Erhitzung, wird der Kunststoff geschmolzen.
· Dosierzone – Die Qualität der Schmelze und Farb werden verbessert.
Der Außendurchmesser der Schnecke bleibt konstant während dieser Zonen, aber die Gangtiefe der Schnecken verringert sich von der Zuführungszone bis zu der Dosierzone. Der Flügel der Schnecke komprimiert das Material gegen die Innenseite des Laufes. Diese Bewegung erzeugt viskose Wärme. Obwohl es den Heizbänder auf dem Lauf gibt, ist diese viskose Wärme die primäre Wärme, um den Kunststoff zu schmelzen. (Die Hauptfunktion der Heizbänder ist, um die Temperatur des geschmolzenen Materials aufzuhalten.) Der Kunststoff wird 80% bei der Schnecke und 20% bei den Heizbänder geschmolzen.
Die Düse bildet eine abgedichtete Verbindung zwischen dem Lauf und der Angussbuchse der Form. Die Temperatur der Düse wird normalerweise in der Nähe der Schmelztemperatur der Kunststoffe eingestellt. Die Angussbuchse der Form hat einen konkaven Radius. Die Düse wird in diesen Radius eingesetzt mit der Hilfe eines Festrings. Der geschmolzene Kunststoff wird zu der Form eingeleitet. Am Ersten wird er durch eine Angussbuchse eingeleitet, dann wird er in einem Kanalsystem erreichen. Am Ende wird er eingespritzt in der Form. Dieser Vorgang heißt Plastifizierung.
Wenn das Teil etwa 95% gefüllt ist, dann ist die so genannte erste Stufe der Einspritzung abgeschlossen. Das Teil wird in der Kavität das Gestalt annehmen. Damit beginnt der Vorgang von der Verpackung und Haltephase. Die endgültige 5% des Teils wird durch die Geschwindigkeit und der Druck gesteuert. Die Verpackung und Haltephase wird dauert, bis das Tor verschlossen ist, um die Abmessungen der Teile zu stabilisieren.
Die Zeitdauer der Abkühlung ist abhängig von der Wandstärke, Kunststoff, Schmelztemperatur, Formtemperatur und Schrumpfung. Mit der besser ausgebildeten Struktur und dem effizienten Abkühlungssystem kann man die Kosten der Verarbeitung reduzieren. Das Wasser wird durch die Form eingeleitet, um die Abkühlung zu verbessern. Während der Kühlzeit wird die Plastifizierung erfolgt.
Plastifizierung ist einen Vorgang, um den Kunststoff zu schmelzen und um den nächsten Anguss vorzubereiten. Der Kunststoff wird an einer Hersteller-Spezifikation getrocknet. Der getrocknete Kunststoff wird aus einem Trichter in dem JIT Lader eingeleitet und tritt in die Zufuhrkehle. Die Zufuhrkehle hat eine Wasserleitung, dadurch kann die Blockierung von Kunststoff an dem Zufuhrhals verhindert werden.
Ein Rückschlagventil wird mit der Vorderseite der Schnecke verbindet. Der Zweck des Rückschlagventils wird als Kolben und Extruder gehandelt. Mit dem ausgestatteten Rückschlagventil kann das Material in der Schnecke eingeleitet werden, um den nächsten Anguss vorzubereiten. Während der Einspritzung, kann das Rückschlagventil das Zurückfließen des Materials in der Schnecke verhindern.
Die Form wird geöffnet, wenn der nächste Anguss erstellt wird und die Abkühlzeit abgelaufen ist. Die Form wird langsam geöffnet, um das Vakuum zu entlassen, das durch den Spritzgiessverfahren verursacht wird. Die Teile, die auf der stationären Seite bleiben, werden auch verhindert, mit der Form anzustoßen. Das Ende der Bewegung wird durch die Gestaltung des Teils bestimmt, um die Zykluszeit zu minimieren. Sobald die Form offen ist, wird das Teil in der Regel durch die Auswerferstifte ausgeworfen. Wenn die Auswurfstifte zurückgezogen sind, und alle Kriterien des Formzyklus die Anfangsbedingung des nächsten Zyklus erfüllen.
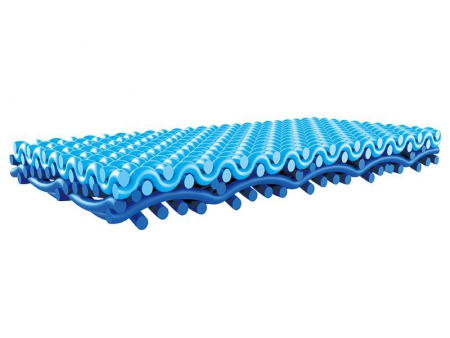